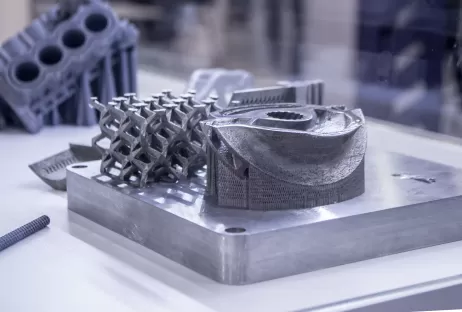
Porque é que a tecnologia FFF (Fused Filament Fabrication), também conhecida como FDM (Fused Deposition Modeling), pode democratizar a impressão metálica em 3D?
Inventada há mais de trinta anos, a fabricação de filamentos fundidos e tecnologia FDM (Fused Deposition Modeling) contribuiu grandemente para o desenvolvimento da fabricação aditiva de polímeros ou compostos.
Revolucionou a impressão em 3D ao tornar possível a construção de peças com geometrias complexas e ocas, com cavidades ou canais integrados. Estas peças foram construídas com base em materiais termoplásticos utilizados sob o formato de fios. A biblioteca dos mais recentes materiais disponíveis para a tecnologia FDM está em constante crescimento e, em determinadas condições, tem potencial para competir com o desenvolvimento da impressão metálica em 3D ao oferecer inúmeras possibilidades de produção.
Como funciona a impressão em 3D FDM?
Na impressora em 3D, o fio termoplástico, normalmente fornecido a partir de bobinas, é primeiro aquecido e extrudido, antes de ser colocado, camada a camada, em cordões, onde o material é necessário, para construir a peça de acordo com a representação digital (ficheiro do modelo em 3D SSL) enviada para a impressora.
Quais são os parâmetros importantes?
As características mecânicas, o acabamento superficial e a qualidade geral das peças produzidas por uma impressora FDM podem ser sensíveis a determinados parâmetros que afetam o resultado e desempenham um papel importante no processo. Estes parâmetros incluem:
- A escolha do material de entre uma vasta gama de materiais termoplásticos, desde os mais simples (PLA, PA, ABS, etc.) até aos mais técnicos, procurados pelo seu elevado desempenho como, por exemplo, PEI, PEEK, compósitos com aditivos orgânicos ou inorgânicos, para obter propriedades específicas, etc.
- A capacidade linear de deposição de material é determinada pelas dimensões do fio, pela temperatura de aquecimento do bocal de extrusão, pela velocidade de deslocação em XY, etc.
- A humidade interna absorvida pelo material. De facto, vários termoplásticos (e particularmente poliamidas) são conhecidos por serem materiais sensíveis à humidade em geral.
O seu comportamento pode ser afetado pela reação de demasiada humidade durante a fase de extrusão a alta temperatura (que pode atingir mais de 350 °C para alguns deles, com risco também de oxidação).
O aspeto e a qualidade das peças podem ser alterados (distorções indesejáveis do material - warping) e as propriedades mecânicas podem ser modificadas.
Para prevenir estes riscos, deve ser prestada particular atenção às condições de armazenamento das bobinas de filamento que devem ser armazenadas numa atmosfera seca como, por exemplo, num armário de armazenamento/secagem sob azoto
A impressão em 3D FDM pode produzir peças metálicas?
A evolução contínua dos diferentes materiais que podem ser utilizados nos bocais reticulados das máquinas FDM começa com plásticos e polímeros termoendurecíveis, seguindo-se as ceras e pós cerâmicos combinados com um ligante e, finalmente, nos últimos anos, surgiram tecnologias exclusivas que combinam pós metálicos e ligantes (Binder Metal e Binder Metal Jetting).
Estas tecnologias permitem, após uma fase de extração de ligantes e sinterização dos pós a alta temperatura, construir peças metálicas com características muito semelhantes às obtidas com métodos de fabricação aditiva metálicos como o SLM (Selective Laser Melting).
A fase de sinterização do pó é efetuada a alta temperatura (logo abaixo do ponto de fusão do metal) e requer uma atmosfera de proteção neutra (muitas vezes árgon) ou uma atmosfera ligeiramente ativa e desoxidante (mistura de árgon com uma pequena percentagem de hidrogénio - 3D Heat Mix, por exemplo).
A impressão em 3D FDM pode democratizar a fabricação aditiva de peças metálicas?
Embora seja possível produzir objetos metálicos com a tecnologia em 3D FDM, existem determinadas limitações a serem consideradas, como:
- A grande retração do volume da peça (após extração de ligantes e sinterização), na ordem de 10 a 20%, o que torna difícil a precisão.
- A limitação da produção a peças pequenas (devido à retração do volume).
- Uma porosidade residual do metal que constitui a peça (de 1 a 5%).
Mas esta tecnologia continua a beneficiar de evoluções constantes para melhorar os seus desempenhos. E, para vários fabricantes, estas desvantagens não constituem uma barreira ao desenvolvimento de determinadas aplicações e peças na fabricação aditiva de peças metálicas, dadas as duas principais vantagens do processo:
- o investimento em máquinas 10 a 100 vezes inferior ao da tecnologia em cama de pó SLM;
- a ausência de riscos de segurança relacionados com a utilização de pós inerentes a outras tecnologias (questão de HSA).
Descubra as nossas soluções
Saiba como a Air Liquide pode ajudá-lo a encontrar a tecnologia de fusão adaptada ao seu projeto de fabricação aditiva.
Tem alguma pergunta sobre Fabricação Aditiva? Por favor preencha o nosso formulário de contacto
Os nossos especialistas responder-lhe-ão em menos de 24 horasMais informação
A fabricação aditiva e as tecnologias de impressão industrial em 3D com gases Air Liquide
A importância do laser na produção de metais
A conceção em 3D liberta a produção de peças de restrições
As tecnologias em 3D são compatíveis com a indústria do futuro e com a Indústria 4.0?
Pode a impressão em 3D ser considerada industrial?
Que materiais podem ser utilizados na impressão em 3D?
Evolução dos materiais e processos: que futuro para a fabricação aditiva?
Perguntas frequentes
Porquê utilizar a fabricação aditiva ou a impressão em 3D e como integrá-la na sua produção?
Como são removidos os suportes na fabricação aditiva?
Quais são as diferenças entre a fabricação aditiva e a impressão em 3D?
Como identificar materiais imprimíveis?
O que é a impressão metálica em 3D?
Que setores utilizam a tecnologia em 3D com mais frequência?
Qual é o papel do gás na fabricação aditiva?
Que processo de impressão em 3D escolher?
Como funciona a fabricação aditiva?