Defeitos de soldadura
Frequentemente, os soldadores têm de enfrentar defeitos de soldadura e resolvê-los. A deteção destes defeitos nem sempre é fácil à primeira vista. A Air Liquide explica-lhe em pormenor os principais defeitos e como evitá-los.
Leitura: 4 min
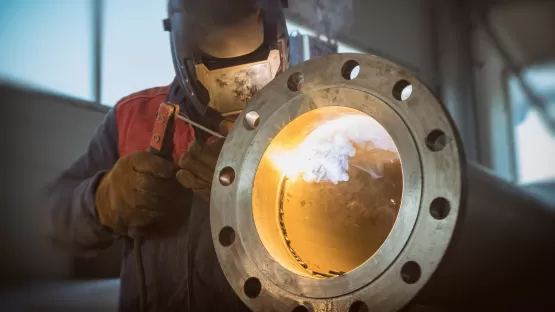
Os materiais a soldar
De uma forma geral, a maior parte dos metais é soldável em TIG/MIG/MAG ou laser com mais ou menos dificuldades metalúrgicas ou operatórias.
Os diferentes tipos de aços
Encontram-se habitualmente vários tipos diferentes de aços:
- Os aços não ligados ou aço ao carbono
- Os aços inoxidáveis ferríticos ou martensíticos
- Os aços inoxidáveis austeníticos
Cada uma destas categorias comporta-se de forma diferente, algumas ligas nestas categorias podem de igual modo apresentar especificidades.
Por conseguinte, é conveniente, na prática, definir com método os domínios operacionais de soldadura para cada um dos materiais e processos utilizados.
Tem alguma questão sobre soldadura industrial?
Os principais defeitos de soldadura
Os defeitos de soldadura podem ser classificados em duas categorias: defeitos ligados ao processo ou aos parâmetros operacionais e defeitos metalúrgicos.
Fissuração a quente
Para garantir a geometria da montagem, as peças são, regra geral, fixadas. O aumento da temperatura no momento da operação da soldadura provoca uma dilatação térmica que se traduz por tensões mecânicas se a peça não se puder dilatar livremente. Em função da energia linear e das propriedades mecânicas da junta associada à liga com um potencial impacto dos elementos da liga acrescentados no metal de adição, o cordão pode fissurar na solidificação.
Porosidades/bolhas
Em função do material, podem surgir porosidades ou bolhas no cordão. Com efeito, o arco elétrico vai maioritariamente quebrar as moléculas presentes e favorecer a passagem de elementos atómicos para o banho de fusão. Na solidificação, é possível que se formem bolhas em função do limite de solubilidade dos elementos na matriz metálica.
A título de exemplo:
- O aço ao carbono só suporta quantidades de azoto muito reduzidas
- O alumínio com o hidrogénio (eventualmente proveniente da humidade do ar ou da camada de alumina)
Cabe referir que a implementação do gás de proteção desempenha um papel importante para prevenir o aparecimento de porosidades. Frequentemente, não é tanto a pureza do gás que está em causa mas sim a posição da tocha, a regulação do caudal, etc. A preparação da superfície é igualmente importante, em particular para as chapas pré-pintadas de aço ou as peças de alumínio.
Defeitos geométricos
A energia linear é um aspeto importante. Mantendo-se constante a velocidade de avanço, importa analisar os parâmetros elétricos para concluir sobre a transferência de calor para a chapa consultando os ábacos que combinam os efeitos cruzados do processo, do tipo de configuração (ângulo, etc.).
A taxa de metal depositado é igualmente primordial para assegurar a boa resistência mecânica.
Uma vez fixados estes parâmetros, importa otimizar a geometria do cordão. Em processos normalizados, o resultado está registado em Especificações e qualificações de procedimentos de soldadura (QMOS/DMOS nas siglas em francês) incluindo todos os parâmetros importantes como o tipo de máquina, a configuração de soldadura, etc.
Há que prestar uma atenção muita particular à:
- Penetração: profundidade máxima da zona fundida, que deve ser suficiente sem ser excessiva com o risco de perfurar a chapa. Em alguns processos, utilizam-se ripas no lado oposto para assegurar uma penetração completa sem colapso. Estas podem ser de cobre arrefecido com água, salvo se este material for proibido pelas normas da construção.
- Forma da penetração: para a soldadura em ângulo, por exemplo, a penetração dita “em dedo de luva” é sinónimo de um risco de falta de penetração na raiz, sendo preferível ter penetrações compactas.
- Controlo da sobre-espessura do cordão: embora seja indispensável, importa limitar a sobre-espessura (ou canal angular), em articulação com os códigos de construção aplicáveis, para otimizar a taxa de deposição e a produtividade.
- Forma do cordão: os ângulos de junção (ligados à molhagem) devem ser tão baixos quanto possível. A título de exemplo, nas montagens sujeitas a fadiga, ângulos demasiado abruptos são suscetíveis de concentrar as tensões e provocar uma rutura.
Para todos estes parâmetros, há calibres ou bitolas que permitem verificar simplesmente os parâmetros geométricos que se podem observar no cordão.
- Regos: por vezes, surgem na borda dos cordões défices de fusão, em casos extremos humping (bossas) que, com frequência, se associam a uma velocidade excessiva ou a uma regulação elétrica imprópria.
Fissuração a frio
A fissuração a frio é a grande preocupação dos soldadores: na realidade, são fissuras que podem surgir em alguns materiais, vários dias depois da soldadura, muitas vezes quando a tensão se exerce ou quando a peça entra em funcionamento.
O princípio é bastante complexo: em função dos materiais (aço, inox ferrítico, por exemplo), é possível que se introduza hidrogénio denominado difusível na matriz metálica durante a soldadura. Estes átomos de hidrogénio vão progressivamente migrar para a junta granular da estrutura e iniciar fraturas quando a tensão se exerce. Assim sendo, é particularmente importante verificar a sensibilidade do material a montar à fissuração a frio para que sejam tomadas as medidas necessárias.
Alteração das propriedades mecânicas
É importante escolher os melhores pares fio gás para assegurar as propriedades mecânicas. Os efeitos de uma concentração acrescida em oxigénio dissolvido ou de uma má transferência de elementos da liga no arco podem ser significativos.
A exemplo do que sucede na soldadura inox austenítica, a oxidação excessiva cria carbonetos de crómio que podem alterar a resistência à corrosão.
Só os parâmetros elétricos corrente/tensão podem exercer uma influência forte sobre as variações do tamanho do grão à solidificação e degradar significativamente os desempenhos mecânicos.
Aspeto da soldadura
Inúmeros parâmetros podem alterar o aspeto do cordão e, portanto, a qualidade. Podemos referir:
- coloração dos cordões em inox se o cordão estiver mal protegido, pelo que importa verificar os parâmetros operatórios, considerar a utilização de um elemento móvel automatizado para proteger o cordão ainda quente depois da passagem do elétrodo
- silicatos: regra geral sob a forma de ilhotas de materiais na superfície. Podem provocar defeitos na soldadura por pontos múltiplos ou criar problemas posteriores após a pintura, por exemplo (escamação)
Mais uma vez, a escolha do par fio/gás é importante.
Em resumo, a formação dos soldadores deve incluir uma inspeção visual final da soldadura para cumprir os critérios de qualidade requeridos.
Tem alguma questão sobre soldadura industrial?
Descubra as nossas soluções
Tem alguma pergunta sobre soldadura industrial? Preencha o nosso formulário de contacto.
Os nossos especialistas responder-lhe-ão o mais brevemente possível.Mais informação
- Corte a laser
- Soldadura por plasma
- Corte por plasma
- O processo de soldadura MIG/MAG (GMAW)
- Capuzes e máscaras de soldadores
- O processo de oxicorte
- Temperatura de fusão de um metal
- Máquina de soldadura
- Metal de adição
- Metal de adição em MIG/MAG
- Processo de arco submerso
- Tochas de soldadura
- Soldadura por resistência
- Soldadura TIG/de metais
- Mistura de gases para a soldadura por fusão
- Soldadura por arco de plasma
- Soldadura por plasma
- Processo De Brasagem
- Cobre e ligas
- Processos de soldadura
- Soldadura por arco elétrico
- Gás inerte para soldadura
- Segurança em soldadura
Perguntas frequentes
- Como regular o débito de gás em soldadura?
- Qual é a diferença entre os processos de soldadura MIG e MAG?
- Como soldar aço galvanizado?
- Como escolher o gás a utilizar em MIG ou MAG?
- Por que motivo utilizar um fio fluxado?
- Como soldar aço?
- Como soldar alumínio?
- Qual é o impacto da pureza do gás de soldadura e corte?
- Quais são os defeitos de soldadura mais comuns?
- Como soldar aço inoxidável?
- Qual é a diferença entre soldadura e brasagem?
- Como escolher o gás a utilizar em TIG ou Plasma?
- Como evitar o consumo excessivo de gás de soldadura?